Propriétés et applications de l'alliage Mg-Re-Zn-Zr
Selon les principes d'alliage, le ND parmi les éléments des terres rares (RE) présente une solubilité relativement élevée dans Mg, contribuant de manière significative à la fois à la température ambiante et à la résistance à haute température. RE mixte (principalement CE) et CE montrent la solubilité la plus faible (0,85%), ce qui profite à la résistance à haute température mais affecte négativement la résistance et la plasticité à température ambiante. LA a l'effet le plus faible, offrant des contributions inférieures à la résistance à la fois à haute et basse température par rapport aux ND et CE.
ZM3 et ZM4 appartiennent au système MG-CE. Les deux alliages partagent des teneurs en RE mixte (riche en CE) et en ZR (voir ci-dessous) mais diffèrent dans la teneur en Zn: ZM3 a un Zn faible (0,2% –0,7%), entraînant une résistance à la température ambiante plus faible, tandis que le ZM4 contient un Zn plus élevé, améliorant la résistance à la température ambiante mais réduisant la résistance élevée à haute température. Les deux alliages présentent une excellente stabilité thermique à 200 à 250 ° C, le ZM3 maintient une résistance presque inchangée jusqu'à 250 ° C. La microstructure telle que castée des alliages MG-CE se compose de composés en phase α et RE aux joints de grains. La taille des grains diminue avec l'augmentation de la teneur en ZR dissoute, améliorant les propriétés à température ambiante. Pour répondre aux exigences de performance standardisées, le ZR dissous doit être ≥ 0,4% pour ZM3 et ≥ 0,5% pour ZM4 (diamètre de grain moyen ≤0,04 mm).
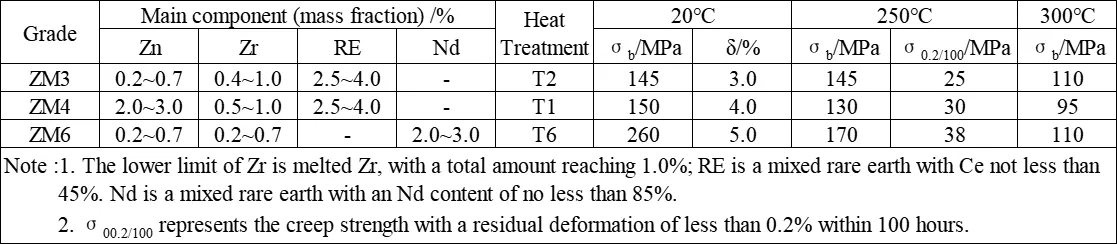
La composition chimique et les propriétés mécaniques à des températures élevées et basse des alliages de magnésium résistants à la série Mg-Re-Zn-Zr
I. Composition chimique et propriétés de l'alliage ZM3

Composition chimique et contenu d'impureté (% en poids) de ZM3
Le système de traitement thermique de l'alliage ZM3: ZM3 est généralement utilisé à l'état comme cast. Lorsqu'il est recuit, le processus recommandé est (325 ± 5) ° C pendant 3 à 5 h, suivi d'un refroidissement par air. La température d'allumage de ZM3 dans l'air est ≥400 ° C, bien que l'inflammabilité dépend des dimensions des parties et de la géométrie. Les particules fines ou la poussière s'allument facilement, tandis que les copeaux d'usinage posent des risques d'incendie inférieurs à moins d'être chauffé au-dessus des points d'allumage. Les sections épaisses nécessitent un chauffage prolongé pour combustion.
Ii Processus de fusion et de coulée de l'alliage ZM3
(1) L'alliage est fondu dans un creuset en acier à faible teneur en carbone pour le soudage. Le processus de fusion des alliages contenant du zirconium est différent de celui des alliages de magnésium contenant de l'aluminium. Il doit être effectué dans le même creuset que le casting. Le transfert vers un autre creuset pour la coulée entraînera une perte de teneur en zirconium. L'alliage est fondu sous la couverture d'un flux composé de chlorures et de fluorures. Pendant le processus d'alliage, les métaux des terres rares ne doivent pas être exposés à des températures élevées dans l'air au-dessus de la surface liquide, et elles ne doivent pas être retirées de la surface liquide pour éviter l'oxydation et la perte. La perte de zinc peut être ignorée, tandis que la perte de terres rares varie en fonction de l'opération de coulée, allant généralement de 10% à 15%. Le zirconium est ajouté sous la forme d'un alliage maître de magnésium-zirconium avec une fraction de masse de zirconium supérieure à 25%. Pendant le raffinage, un flux spécial sans chlorure de magnésium est saupoudré sur la surface métallique. En effet, le chlorure de magnésium dans les flux ordinaires réagira avec les métaux des terres rares pour former des chlorures de terres rares qui précipitent du liquide métallique, provoquant une perte de terres rares. Avant le coulage, le métal est laissé pour se tenir debout pendant 15 à 20 minutes pour permettre au flux de se séparer du métal et de précipiter avec des composés insolubles. Ensuite, la température est réduite au niveau requis pour couler les pièces moulées. Au moins 15% à 20% de la fonte d'alliage devraient rester au fond du creuset pour empêcher le scories, le flux et le zirconium insoluble d'être versé dans le moule.
(2) Pendant le processus de préparation de l'alliage, la contamination par des éléments tels que l'aluminium, le fer, le silicium et le manganèse doit être empêchée, car ces éléments entravent l'effet de raffinement des grains du zirconium.
(3) En raison de la faible solubilité du zirconium et de sa tendance à former des composés avec divers éléments d'impureté et à être perdue, la quantité de zirconium ajoutée doit être de 3 à 5 fois la teneur en zirconium requise dans l'alliage.
(4) Le degré de raffinement des grains est étroitement lié à la teneur en zirconium dissous dans l'alliage. Dans le même temps, la teneur en zirconium a un impact significatif sur les propriétés de traction de l'alliage. Par conséquent, la technologie de fusion et le contrôle de la température sont extrêmement crucial.
Iii. Propriétés physiques de l'alliage ZM3
L'alliage ZM3 n'est pas magnétique. Sa plage de température de fusion est de 590 à 645 ℃. La conductivité thermique λ est de 117 W / cm · ℃ à 100 - 300 ℃. La densité γ est de 1,80 g / cm³. La résistivité ρ à 20 ℃ est de 73 nΩ · m. La capacité thermique spécifique et le coefficient d'extension linéaire de l'alliage ZM3 sont indiqués dans le tableau suivant.

Le coefficient d'expansion linéaire de l'alliage ZM3

La capacité thermique spécifique de l'alliage ZM3
La microstructure de l'alliage ZM3 en état comme cast est constituée d'une solution solide Mg et des composés en blocs distribués aux joints de grains. En cas de corrosion profonde, une ségrégation intragranulaire de ZR peut être observée. Une teneur en ZR plus élevée entraîne une taille de grain plus fine de l'alliage et une tendance inférieure aux composés à se former dans les dendrites. Après recuit à 325 ° C pendant 3 à 5 heures, certains composés se précipitent sous forme de petites particules à l'intérieur des grains. L'alliage de magnésium ZM3 a une excellente résistance à la corrosion dans l'air sec, mais sa stabilité chimique est médiocre dans l'air humide, l'eau (en particulier l'eau de mer), et il réagit vigoureusement avec la plupart des acides inorganiques. Dans les atmosphères industrielles, la résistance à la corrosion du magnésium est similaire à celle de l'acier à carbone moyen. Le film d'oxyde de magnésium n'est pas dense, donc un traitement de surface est nécessaire pour une utilisation à long terme dans des conditions atmosphériques. Les alliages de magnésium sont stables contre l'acide sélénique, les fluorures et l'acide hydrofluorique, formant des sels insolubles. Contrairement à l'aluminium, les alliages de magnésium ne réagissent pas avec l'hydroxyde de sodium et sont également stables dans l'essence, le kérosène et l'huile de lubrification. Le magnésium est l'un des métaux les plus électronégatifs et ne doit pas être directement assemblé avec des pièces en alliages d'aluminium (à l'exception des alliages al-MG), des alliages de cuivre ou de l'acier, car cela peut provoquer une corrosion électrochimique. Le fer, le cuivre, le nickel, le silicium, les chlorures et d'autres impuretés, ainsi que certains défauts de coulée, peuvent réduire la stabilité de la corrosion des alliages de magnésium. Le ZR dans l'alliage peut affiner la taille des grains et éliminer les effets nocifs des impuretés, améliorant considérablement la résistance à la corrosion de l'alliage.
Iv. Processus des propriétés de l'alliage ZM3
(1) formant des performances.
L'alliage ZM3 a une excellente procédabilité de coulée, avec une température de coulée de 720 à 800 ° C. L'alliage a de bonnes propriétés de remplissage, et sa fluidité, mesurée par la longueur de la barre d'essai coulée, est de 300 mm. Il n'y a aucune tendance à former une porosité microscopique pendant la solidification. La première fissure dans le test de tendance de fissuration thermique se forme à une largeur d'anneau de 12,5 à 15 mm. Le taux de retrait linéaire est de 1,3%.

Propriétés de traction typiques des pièces moulées en alliage ZM3 à température ambiante et à haute température
(2) Performance de soudage.
L'alliage peut être soudé par le soudage à l'arc d'Argon et a une bonne performance de soudage de réparation. La contrainte interne doit être éliminée après le soudage, et la qualité interne et l'inspection des fissures de surface doivent être effectuées après le soudage.
(3) processus de traitement thermique
L'alliage n'est recuit que si nécessaire.
(4) processus de traitement de surface
La surface de la coulée doit être chimiquement oxydée pour former une mince couche de protection. Avant le traitement de l'oxydation chimique, la coulée doit être sablée et dégraissée. Selon les différentes utilisations des pièces, l'huile ou la protection de la peinture doit être effectuée après un traitement d'oxydation.
(5) Performances d'usinage et de broyage
L'alliage a d'excellentes performances d'usinage et peut être usinée à une plus grande profondeur de coupe et à une très grande vitesse par rapport aux autres métaux. La puissance requise pour éliminer une certaine quantité de métal est inférieure à celle de tout autre métal. Pendant l'usinage, d'excellentes surfaces lisses peuvent être obtenues sans broyage ni polissage, que ce soit avec ou sans coupe de liquide.
V. Applications de l'alliage ZM3
L'alliage ZM3 est largement utilisé dans les pièces du moteur, les accessoires et divers boîtiers.